PRIMAFORM
PRESS BRAKE
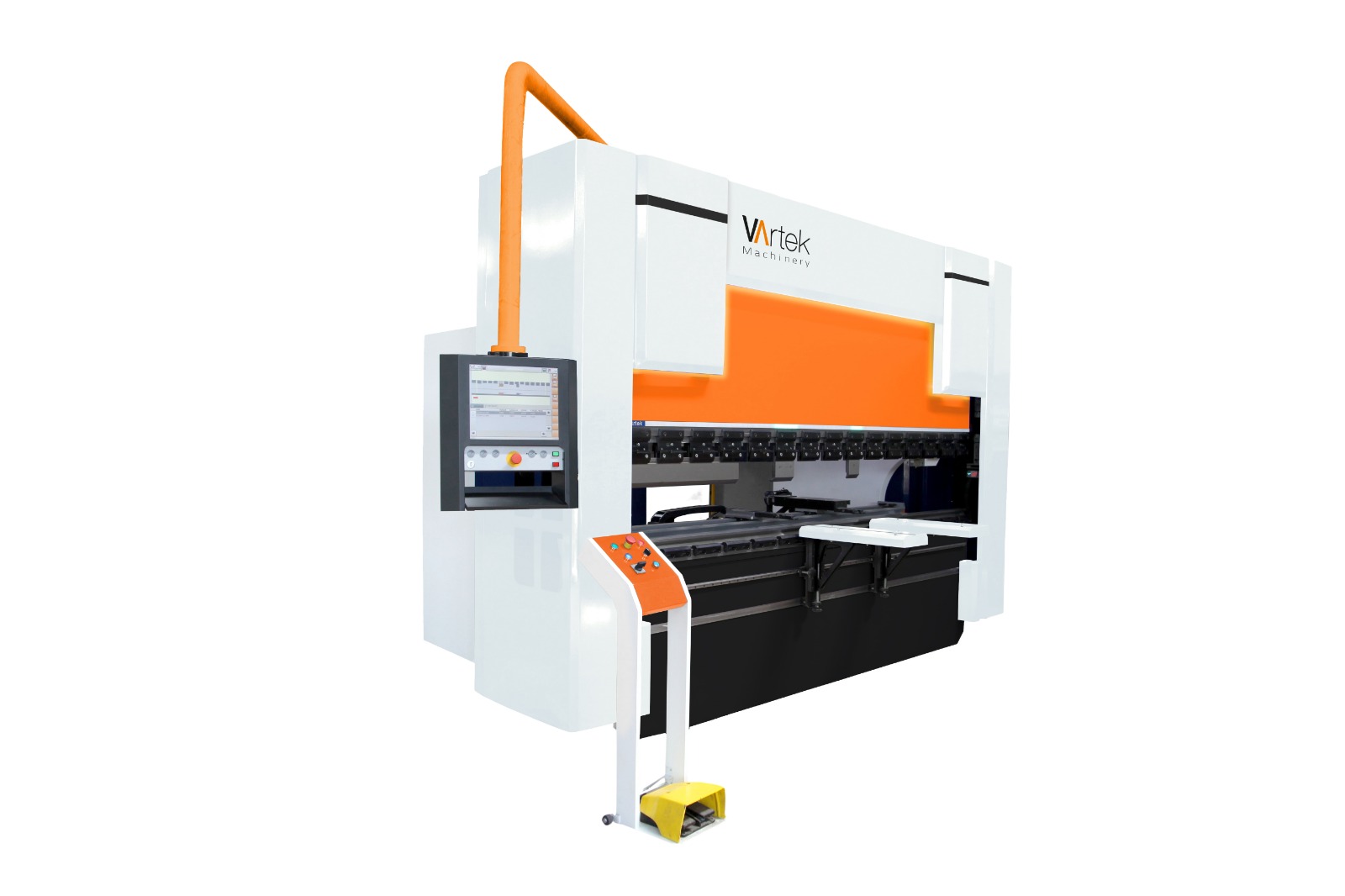
Cnc Control
We know how hard it is to find experienced press brake operators, how hard it is to train rookie operators and our primary goal was to create a control that can be run by anyone. And when we say anyone, we mean it! Please ask your local dealer for a hands on demo and you will see what we mean!
Main
Main
Whether you want to form a part by air bending, bottoming or hemming, PrimaForm’s advanced angle calculation formula, precise servo hydraulic system and electronic linear scales ensure you get the right part every time.
The editable material database on PrimaForm lets you add as many material as you want and even allows you to record the springback of each material so the control can autocorrect angles to compensate for springback.
Before we designed PrimaForm, we wanted to fully grasp the challenges and shortcomings that the operators are facing in Precision sheet metal shops and talked to many operators during the process.
Main points every press brake operator emphasized were;
- Easiness of setting up the machine for the next batch
- Setting up the tooling stations in the right places so it matches with the backgauge fingers when forming the part
- An easy way to turn customer drawings into part programs without interrupting product runs.
- Choosing the right tooling for the right job.
- Running prototypes without scrapping high value materials like stainless steel and aluminum.
We already had the foundations of a solid offering with precision, repeatability, consistency and dependability on our PrimaForm and we implemented these requests from our customer base and created the new PrimaForm.
Your Companion
Your Companion
Creating a simple yet elegant companion for you was our primary goal. We hope you like the features below we designed for your production to be more efficient and your products to be flawless.
2D or 3D
2D or 3D
On its 17″ beautiful and colorful touchscreen, a large canvas will display your part and will let you easily manipulate with taps and touches.
DXF IMPORT
DXF IMPORT
Just load your DXF directly to the control or on the offline software and watch NexT magically transform a flat drawing in to a 3D part.
If you are creating your DXF on SolidWorks, NexT will read all the embedded information in the DXF like angle, allowance, radius, thickness and material type and will create a full 3D part without you touching a thing.
Tooling Stations
Tooling Stations
Coupled with VisioForm LED system, you will literally spend two minutes setting up your machine for the next job
Offline Software
Offline Software
You can prepare your part programs or import your DXFs on your PC and transfer them either through a network connection or with a USB thumb drive without stopping your press brake what it does best, running parts!
Auto Tooling
Auto Tooling
Even worse, you may end up damaging your tools. This scenario is more common than you think and that is the reason we designed auto tooling feature on NexT.
Once you finish drawing or importing your part, all you need to do is to hit autotooling button and NexT will offer the right punch and die. Stress free!
User Interface
User İnterface
This is why we spent a great deal of time creating our user interface, making it simple yet elegant, powerful yet easy to grasp.
Your Companion
Tool Clamps
Different jobs require different tools and frequently changing tools on a press brake with a clunky clamp system is no fun.
We agree and for this reason, we have equipped PrimaForm with the easiest tool changing system you can find. Just mount your punch into the holder vertically and press the clamping button. The system will auto-seat and auto-align. You are done!
PrimaForm’s high precision punch and die clamps use industry leading, CNC deep hardened Wila punches and dies. This ensures top accuracy whatever the material is and whatever the job is.
VisioForm
2D or 3D
Enter VisioForm! Our unique tool locator is a strip of LED lights that sit right above the punch clamp and will help you set up your tools easily by lighting up the exact spot you need to mount your tools.
Along with the vertical punch mount ability, VisioForm makes it a breeze to set up your tooling stations. But VisioForm does not stop there and also continues to guide you during the bending process. For each bend, VisioForm will light up the correct tool station so you will know where to gauge your part without even looking at your control’s screen!
Offline Software
DXF IMPORT
You don’t even have to program your part manually. If you have a DXF drawing of the part, NexT can process that flat DXF and turn it into a full blown 3D part program!
DFX drawings exported from SolidWorks* will have crucial information like thickness, type of material, angle, allowance and radii automatically embedded and NexT can read all that information and create a fully formed product to run immediately without any intervention from you.
Autotooling
Autotooling
Let NexT choose the right punch and die with one touch of a button. When you program a part, NexT’s autotool feature will search your tool library and will offer you the right punch and die for the job in hand.
Backgauge
Offline Software
PrimaForm’s multi axis backgauge also allows you to easily bend tapered (conic) parts without the hassle of marking the bending lines.
Crowning
Auto Tooling
Hydraulics
User İnterface
Auto Stop-Start
Auto stop-start function stops all the electric motors when the machine is left idle for a specified time and starts right back when the pedal or start button is pressed.
This feature not only reduces your electric bill and help save the environment but also prevents the hydraulic oil from reaching high temperatures therefore keeps the angles consistent from the start of the day to the end.
Remote Diagnostics
All NexT controls are equipped with remote diagnostic feature and in the unlikely event of an issue, our engineers can remotely connect to your machine and diagnose any issues you might have.
STANDARD & OPTIONAL EQUIPMENTS
Standard Equipments
- Rigid frame designed on SolidWorks with stress and deflection analysis, welded by certified welders and machined to 0,01 mm precision in single piece.
- NexT 3.0 17″ 2D/3D graphic touchscreen control.
- Dependable servo hydraulic system provided by Hoerbieger.
- Honed, chrome covered cylinders with high precision ground pistons.
- Y1-Y2 synchronized hydraulic cylinders running on dual ram guides on each side for smooth ascend and descend.
- 6 axis backgauge (X1,X2,R1,R2,Z1,Z2) running on ballscrews with servo motors and independent finger blocks to easily gauge complex parts and tapered pieces.
- VisioForm LED bend guide system.
- Hydraulic punch holder with vertical mount, auto seat and auto align function.
- Hydraulic die holder with one touch lock mechanism.
- High stroke and daylight for deep box/panel bending.
- 500 mm throat depth to utilize full length and deep bends.
- High resolution linear scales with an accuracy of 0,01 mm for precise bending.
- Automatic crowning of die bed for even angles along full length of bend.
- Front support arms sliding on linear guides to easily gauge small parts.
- Oil coolant to maintain optimum oil temperature and consistent bends in long runs.
Optional Equipments
- Front laser guards for finger protection.
- Custom design throat, stroke and daylight.
- CNC controlled bending aids in front to easily handle large plates.
- Real time angle measurement and correction system.
- Large selection of punches and dies.
- Tandem Preparation
- Automatic Lubrication System
Easiest tool changing system
Visioform
ATF backgauge
DXF Import & Offline Software
Autotooling
Auto Stop-start
© 2018 Vartek Machinery All rights reserved